
As we strive for a more sustainable and energy-efficient world, the importance of software in enabling this transition cannot be overstated. From optimizing renewable energy generation and consumption to enhancing energy storage and distribution, empowering smart cities and facilitating energy-efficient buildings, software solutions are at the forefront of driving transformative change. With collaboration between technology experts, policymakers, stakeholders, and a commitment to innovation, we can harness the power of software to accelerate the global energy transition, paving the way for a greener, more sustainable future for generations.
We are firm believers that software plays an important role in the energy transition, both data driven analysis and control play the role of a platform that makes the technological bridge between data and energy.
Solution
aug.e EMS can fill this gap between data usage and energy management. To overcome these challenges, an extensive use of data analysis, pattern recognition and problem optimization will be captured inside a powerful control strategy, called Model Predictive Control (MPC), that optimizes system performance by considering predictions of future system behavior.
Indeed, the cloud has more information than the local assets and the EMS is optimizing all data to an optimal use of the assetsby means of MPC, forecasts, constraints (hard/soft) and measurement feedbacks. But what is a MPC ?
“Model predictive control is a method to calculate control actions based on solving a constrained optimization problem over a finite time horizon.”
We can consider it as the brain of the whole energy system.

By utilizing real-time data and forecasting models, MPC continuously adjusts control actions to ensure optimal system operation while adhering to constraints. MPC incorporates optimization algorithms, feedback control, and dynamic models to deliver near-optimal control strategies in real-time, enabling efficient energy management and response to changing conditions. It can be visualized by a multi-layered control system which runs at different sample time.
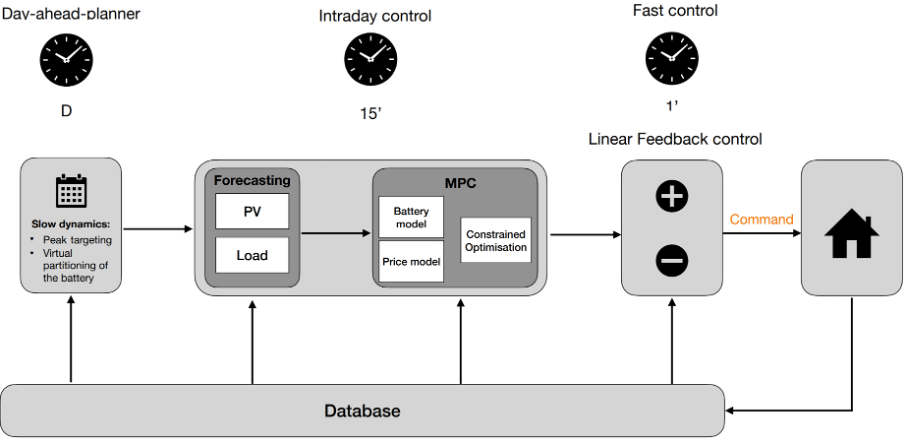
Indeed, the day ahead planner is acting on the global daily control system in order to meet a monthly target whereas the intraday control focuses on the daily target by mean of 15min time step control and finally, an embedded 1min control is ensuring that the 15min target will be met as best as possible during that period and ensures the constraint limits are met at any moment of the day.
EMS value for Hybris project
As the brain of a whole, the EMS role is approaching the coordination of every other system such as building asset telemetries, HESS storage system measurements and the high-level HESS advanced analysis control planner.
Basically, the EMS role is to enable the control of the large flexibility given by the hybrid energy storage system, which is composed of the LTO and AORFB batteries. In fact, the combination of the two C-rate systems offers us the possibility to optimally steer the batteries accordingly to the different electricity market dynamics and use cases.

For instance, arbitrage + self-consumption and monthly capacity shaving strategies will typically be used within a quarter and daily timeframe whereas imbalance and FCR would need a quicker reaction of less than 1min.
Furthermore, islanded mode operation and demand response use cases are two fast reactions steering as well, generally the LTO with its high power capacity will be used for fast dynamic control and the AORFB with its high energy capacity will be used for slow dynamic control.Let’s get insights into the 2 different battery technologies included in the HESS container solution.
-AORFB battery details:

-LTO battery details:

Therefore, communications between different party’s services plays a crucial role in the whole HESS optimization and control system services, with a general structure stated as follow:

The general structure gives an overview over the principal components which are:
- The INMS Scada, PMS and battery BMS specified as the HESS battery system. Its main roles are to transfer the battery I/O from and to third party clouds then ensuring the security and integrity of the whole battery system.
- The ABMS will compute daily inputs to be used inside the day ahead planner control. Optimizing by this means the battery usage and prolonged its life cycles.
- The EMS, which will act as a central data aggregator and supervisor of the whole system. It will provide different services for different pilot sites all around Europe.
- The field device telemetries which represent the building consumption loads, PV production and EV charging stations.
Let’s go through the communication structures of the different sites to define the use cases for each of them.
IT site:

The Italian site will take place in Messina, Sicily (IT). The HESS battery energy system container will be shipped and placed within a small local energy community where the following services will be made available by the EMS:
- Basic energy management services (Arbitrage, Self-consumption, and Peak shaving)
- Islanded mode (Disconnection from the grid and using battery energy as a stand-alone source)
- SAIFI reduction (Power interruption avoidance algorithm)
- Demand response service (Turn On/Off controllable loads within the building as well as EV charging stations)
One can see that CNR/SAE will have a local supervisor called “CNR/SAE Scada” which has 3 specific functionalities:
- Communicates with the EMS cloud through their onsite gateway. The scope here is to be able to retrieve building data, send it to the EMS cloud and transferring control commands to the controllable loads like HVAC, heat-pumps, and charge poles.
- Enabling the grid contactor control for getting the whole system into islanded mode, enabling FCR and power interruption reduction control.
- Serves as energy community monitoring dashboard.
BE site:

The Belgian demo site will take place in Brasschaat, BE and the main goal is to evaluate the impact of using battery’s basic services (arbitrage, self-consumption and peak shaving) with enabling energy sharing between two commercial buildings in the same business park. One is a nail polish factory and the other is a renovated military barrack using for electromechanical applications.
Indeed, with the first building equipped with large amount of solar panels (258 kWp), one can charge the battery during the day when PV energy is at its highest but even more, the production surplus can be sent to support consumption of the second building which doesn’t have any PV installation to share the high amount of PV energy between them and therefore acting as a small energy community.
NL site:

For the Netherlands site it was decided to run a full hardware in the loop simulation meaning of emulating the building consumptions with its energy assets. The HESS battery and control will be done in real time while keeping the existing communication structure between all the partners in order to still providing the different services.
The scope of this “virtual site” is to assess a digital twin model of the real system with all the implied dynamics from electricity consumptions to PV generation, EV charging stations and virtual HESS battery model which will act on each other as a whole. Furthermore, the grid dynamics as well as frequency will be emulated thanks to historical data, building’s nominal parameters and asset’s specifications.
Conclusion
In conclusion, we saw that hybrid energy storage system is relevant as an actual world economic and environmental game changer. Paving the path to a more sustainable future and enabling local energy communities to be built around a basic “energy block” which is composed of a hybrid storage solution mixing two battery technologies, the LTO with high power capacity and AORFB with high energy capacity. Moreover, energy sharing, and self-sufficient capacity will have a big role to play as well for future communities. In this regard, an orchestrator here present as the EMS (energy management system) will have to aggregate the on-field data, analyzing them using machine learning techniques and supervising all the interactions between different and complementary systems.